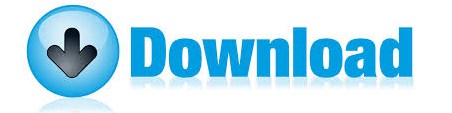

The utilization of metal injection molding for stainless steel is steadily increasing in the automotive and medical instruments sector. These materials are produced from elementally blended or pre-alloyed stainless steels, including ferritic, austenitic, and precipitation hardening grades. The metal injection molding help in enhancing the strength, achieving high densities, corrosion resistance, and flexibility of stainless steels. Stainless steel components that are employed in metal injection molding possess high wear & corrosion stability. It is widely used injection molding material. Stainless steel has good stiffness, wear, and corrosion resistance properties. In 2019, stainless steel segment led the market. The metal injection molding offer benefits such as resistance to wear & corrosion, thermal stability, high mechanical strength, and dimensional stability.īased on material, the global metal injection molding market is segmented into stainless steel, low alloy steel, soft magnetic material, and others. The metal injection molding helps in overcoming this issue with the formation of the net shape parts in the tool. When a metal alloy is chosen for a specific application, the geometry of the component gets limited by the cost of shaping operations. Metal injection molding focusses on quality and precision, as well as the process is closely monitored to meet the requirements. Metal act as a good substitute for plastic and ceramics components that are incapable to perform as per requirement.

Metal injection molding is a flexible, cost effective, and innovative process that provides versatility to the product designers and production engineers while using metal alloys. The global metal injection molding market was valued at US$ 2,458.68 million in 2019 and is projected to reach US$ 4,338.52 million by 2027 it is expected to grow at a CAGR of 7.35% from 2019 to 2027. 03, 2021 (GLOBE NEWSWIRE) - The "Metal Injection Molding Market Forecast to 2027 - COVID-19 Impact and Global Analysis by Material and Industry Vertical" report has been added to 's offering.
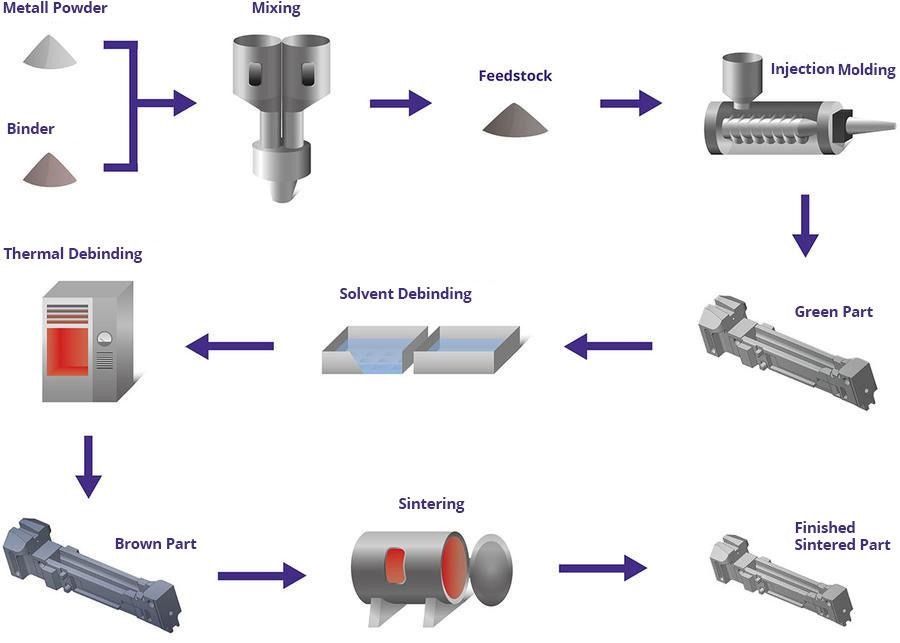
Additionally, Ceramics and Metal Alloy Injection Molding can combine several machined or cast components into one cost-effective product eliminating several manufacturing steps.Dublin, Aug. This injection molding process allows to economically compete with large net shaped process techniques such as Investment Casting. Primary materials using water based agar binding systems are Stainless Steel, Alumina, Zirconia, Steatite and other metal alloys. Due to the relative low molding pressure and temperature required for water based agar binder, soft tooling may be employed in place of hardened tools for production runs less than 10,000 parts. For an example the average tensile properties of the 17-4PH stainless steel alloy is compared against wrought and cast properties, tensile properties were essentially equivalent to wrought and exceed typical cast properties. Many of these applications require demanding mechanical properties. This technology is applied to a variety of automotive applications such as EGR System, Exhaust System, Oxygen Sensors, Electrical Components, Engine Components, etc. As a result, savings are achieved not only by eliminating machining and other processing steps but also by reduced development and inventory costs. Other significant advantages of this system are a clean and rapid debind and the ability to mold into soft tooling. A new water based agar binder system for metal and ceramic injection molding has been developed that offers the ability to produce large thick parts in range of 1 to 2 kg which are competitive with those produced by investment casting. Traditional application for metal injection molding or ceramic injection molding have been small net shaped parts exhibiting design and economic benefit over wrought or cast components.
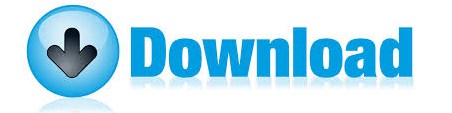